#HTE
Design Rules for 3D Printing
Introduction
Anything can be designed in the digital space, but not everything can be 3D printed.
When you design a part for 3D printing - whether it’s for prototyping or for manufacturing end-use products - certain limitations apply. These limitations have to do with the basic mechanics of each additive manufacturing process (and the laws of physics).
In this article, we summarize the most important rules and process restrictions you must keep in mind when you design parts for each of the main 3D printing processes. We also describe the key strengths and limitations of each technology to help you get the most out of your designs.
If you are not sure which 3D printing process or material is best for your application, visit our previous articles here and here.
Keep this infographic near you while designing and use it as a quick reference:
Designing for FDM
In Fused Deposition Modelling (FDM), an object is built by selectively depositing melted material in a predetermined path layer-by-layer. The materials used in FDM are thermoplastic polymers that come in a filament form.
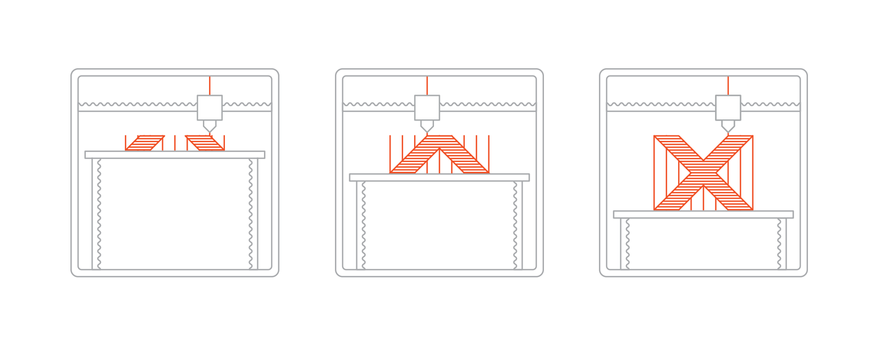
The main design limitations in FDM come from the shape and size of the deposited melted strings of plastic material. These have a typical width of 0.4 to 0.5 mm and a typical layer thickness of 100 to 300 µm.
The recommended minimum wall thickness of FDM is 1 mm, but protruding features and pins need to be larger (the recommended minimum is 2 mm and 3 mm respectively). Another limitation of FDM is the need for support structures: the melted material cannot be deposited on thin air. Any wall that has an inclination greater than 45o from the vertical needs to be supported. Support structures are usually printed in the same material as the base part, but dissolvable supports that provide a better result are becoming more and more common. Surfaces printed on support structures usually have a lower finish than the rest of the part, so it is recommended to avoid them altogether if possible, by thinking about the part orientation on the machine while designing.
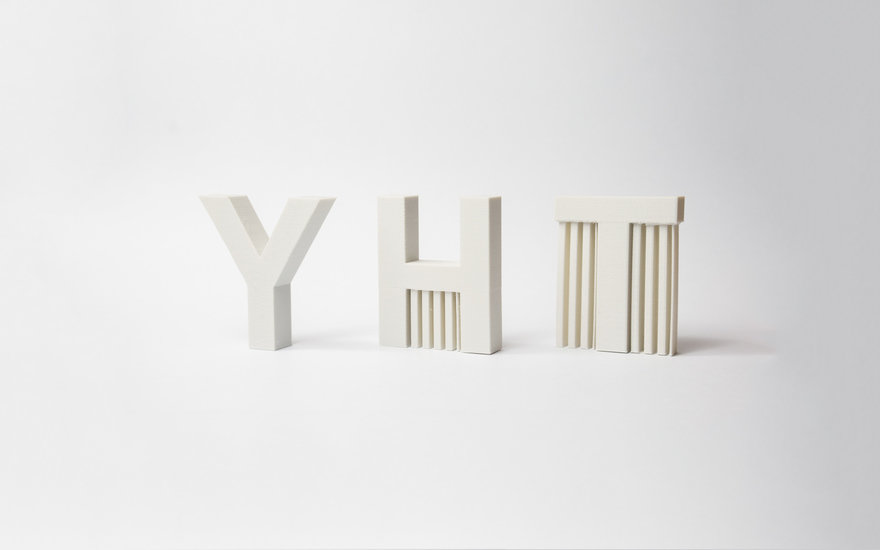
A common misconception about FDM is that a lower layer thickness is always better. A lower layer thickness than the standard (which is 200 µm) should be used only when you design parts with very small features or with significant curvature, as it reduces the “stair-stepping” effect.
Here is a summary of other important FDM printer parameters:
-Typical build size: 200 x 200 x 200 mm (up to 1000 x 1000 x 1000 mm)
-Common layer thickness: 50 to 400 µm
-Support structures: Required (critical angle 45°)
-FDM materials: Thermoplastics (PLA, ABS, Nylon, PETG, ULTEM - see more)
For more details on designing parts for FDM, visit the article here.
Designing for SLA/DLP
In Stereolithography (SLA), an object is created by selectively curing a polymer resin layer-by-layer using a UV laser beam. Direct Light Processing (DLP) is a similar technology that uses a projector instead of a beam. The materials used in both SLA and DLP are photosensitive thermoset polymers that come in a liquid form.
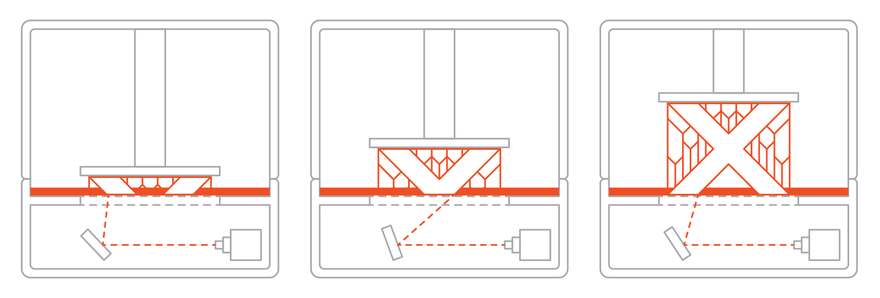
SLA and DLP can produce some of the most accurate 3D printed parts with very fine details, as the light source can solidify material very accurately. With this process, features can be produced that have dimensions down to 0.2 mm and walls with a thickness of 0.5 mm (sometimes even smaller).
SLA and DLP are also known for producing parts with a very smooth surface finish that resembles injection molded parts. Keep in mind though that support structures are also required here (the critical angle here is again 45°).
Support in SLA/DLP has a tree-like structure. At the points of contact, small marks will be visible on the part and manual post-processing is required to remove them. For this reason, keep all features that require the highest dimensional accuracy on the same side of the part if possible.
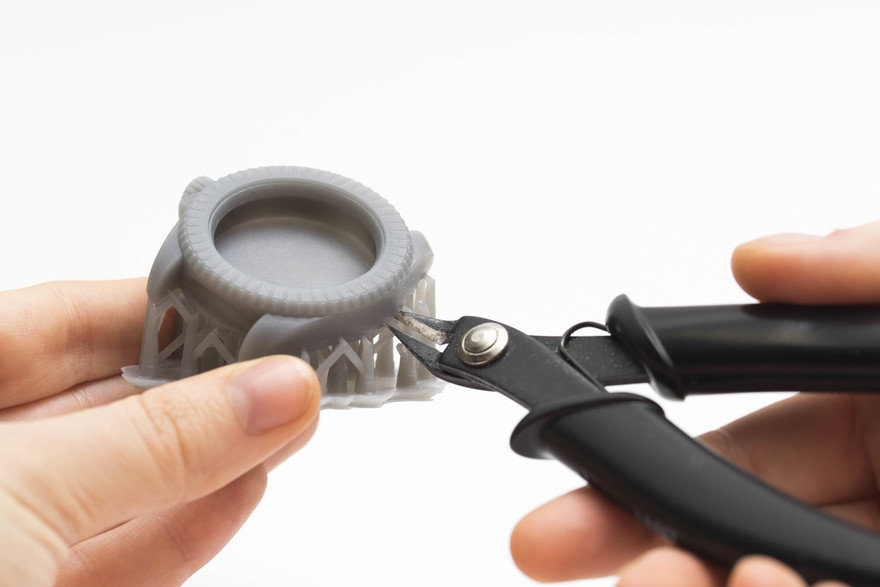
Here is a summary of other important SLA/DLP printer parameters:
-Typical Build size: 145 x 145 x 175 mm (up to 1500 x 750 x 500 mm)
-Typical layer thickness: 25 - 100 µm
-Support structures: Always required
-SLA materials: Thermoset resins (standard, ABS-like, PP-like, rubber-like - see more)
For more details on designing parts for SLA/DLP, visit the article here.
Designing for SLS
In Selective Laser Sintering (SLS), a laser passes over particles of a polymer powder, fusing them together and building a part layer-by-layer. The materials used in SLS are thermoplastic polymers that come in a powder form.
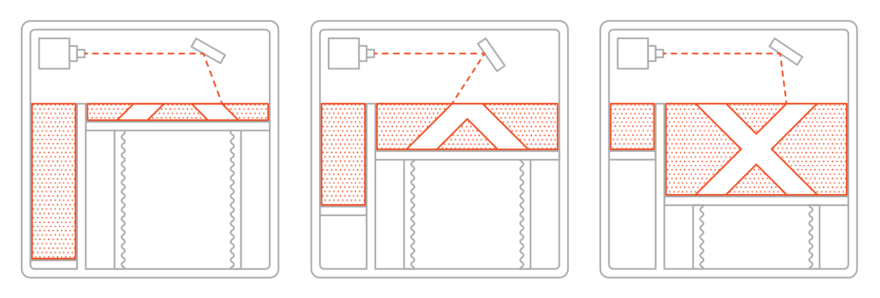
SLS can produce parts with good details and great accuracy: the minimum feature size that can be produced with SLS is 0.7 to 0.8 mm. Holes must have a minimum diameter of 1.5 mm though, to prevent over-sintering.
A key advantage of SLS is that it needs no support structures. The unsintered powder provides the part with all the necessary support. For this reason, SLS can be used to create freeform geometries or interlocking assemblies that are impossible to manufacture with any other method (leave a 0.3 mm gap between the moving parts).
Beware though that warping is an issue in SLS, so it is not recommended to 3D print parts with large length-to-width aspect ratio with SLS.
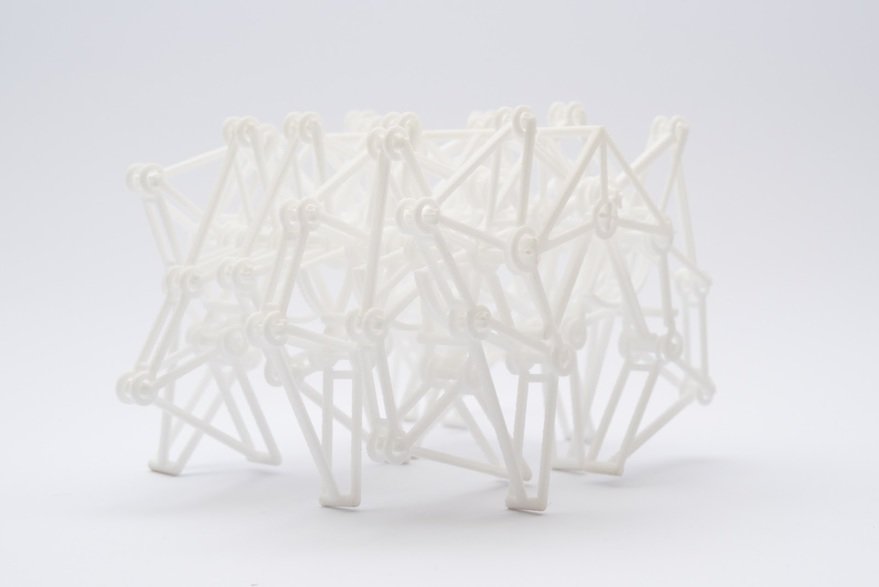
Here is a summary of other important SLS printer parameters:
-Typical build size: 300 x 300 x 300 mm (up to 750 x 550 x 550 mm)
-Support structures: Always required
-Typical layer thickness: 25 - 100 µm
-SLS materials: Thermoplastics (Nylon, TPU, composites - see more)
For more details on designing parts for SLS, visit the article here.
Designing for Material Jetting
In Material Jetting, a printhead (similar to the printheads used for standard inkjet printing) dispenses droplets of a photosensitive material that solidifies under ultraviolet (UV) light. The materials used in Material Jetting are thermoset photopolymers (acrylics) that come in a liquid form.
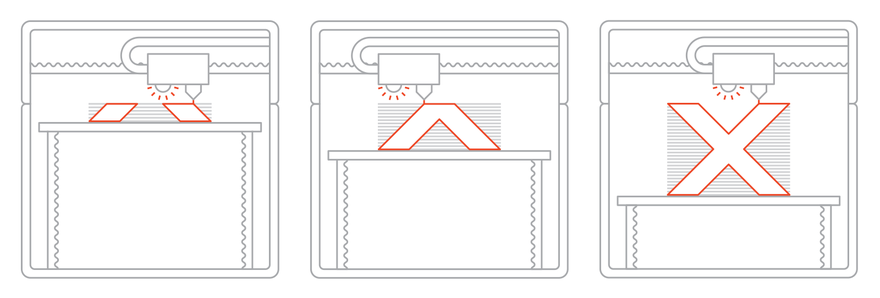
Material Jetting is considered the most accurate of all 3D printing technologies and can produce parts with very smooth injection molding-like surface finish.
Due to the nature of the material dispensing though, the recommended minimum wall thickness and feature size are 1 mm and 0.5 mm respectively, which is larger than SLA/DLP.
Support structures are always required in Material Jetting, but they are printed in a secondary dissolvable material that can be easily removed after printing, leaving little to no remnants.
A key advantage of Material Jetting is the ability to produce accurate multi-material and multi-color prints that represent accurately end-use products. To designate a different material or color to particular areas of the part, the model must be exported as separate STL files (for single color/material) or accompanied with an OBJ or VRML file (when blending colors).
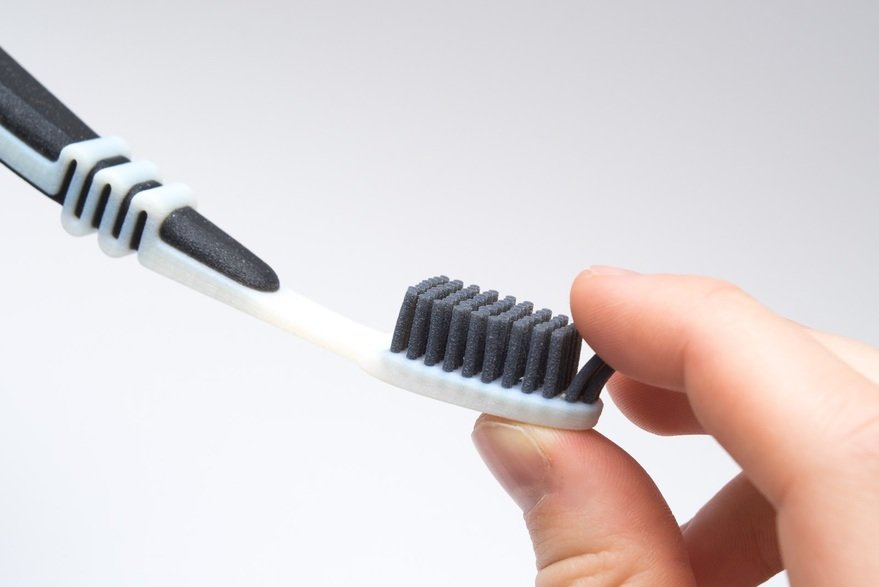
Here is a summary of other important Material Jetting printer parameters:
-Typical build size: 380 x 250 x 200 mm (up to 1000 x 800 x 500 mm)
-Support structures: Always required (but soluble)
-Typical layer thickness: 16 - 32 µm
-Materials Jetting materials: Thermoset resins (ABS-like, PP-like, rubber-like - see more)
For more details on designing parts for Material Jetting, visit the article here.
Designing for DMLS/SLM
Direct Metal Laser Sintering (DMLS) and Selective Laser Melting (SLM) are similar technologies that use a laser to scan and selectively fuse (or melt) the metal powder particles, bonding them together. The materials used in both processes are metals that come in a powder form.
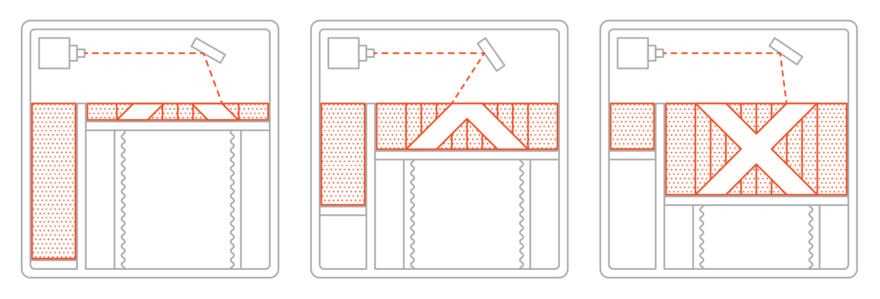
DMLS and SLM machines are high-end industrial systems that have great accuracy. The minimum achievable wall thickness and feature size are 0.4 and 0.6 mm respectively.
Support structures are always required in metal 3D printing to prevent warping and to anchor the part on the platform and they are printed in the same metal material as the base part. Simulations and topology optimization algorithms using specialized software are often employed to minimize the amount of support, as are difficult to remove.
Since DMLS/SLM requires considerable engineering effort and has a high cost, currently it is mainly used in high-end applications. The key strengths of the technology lay on the opportunities of manufacturing highly-optimized lightweight structures and consolidating multiple components of an assembly into a single part.
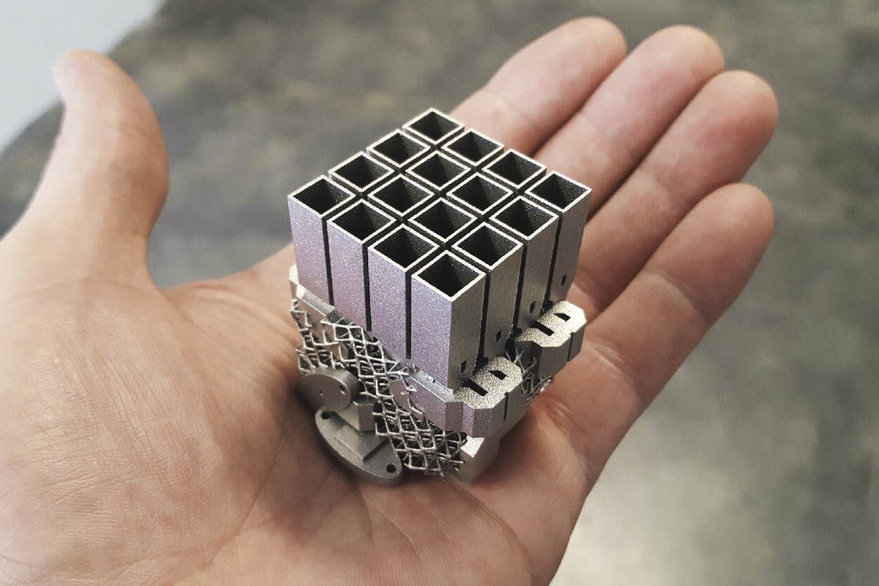
Here is a summary of other important DMLS/SLM printer parameters:
-Typical build size: 250 x 150 x 150 mm (up to up to 500 x 280 x 360 mm)
-Support structures: Always required
-Typical layer thickness: 20 - 50 µm
-SLM/DMLS materials: Metal and alloys (stainless steel, aluminum, titanium - see more)
For more details on designing parts for DMLS/SLM, visit the article here.
Designing for Binder Jetting
In Binder Jetting, an adhesive binder is selectively dispensed onto a powder bed, bonding the particles together one layer at a time to form a solid part. The materials used in Binder Jetting are metals, sand, ceramic or polymers that come in a powder form.
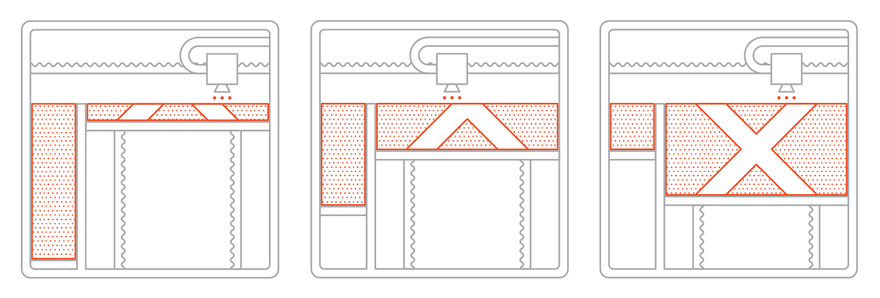
Binder Jetting is not recommended for manufacturing parts with fine features and small details (the recommended minimum wall thickness is 2 mm). This is because the as-printed parts are fragile and need to be strong enough to survive the post-processing step before they gain their good mechanical properties.
The strengths of Binder Jetting lay on the fact that printing occurs at room temperature: thermal effects, like warping, are not an issue here so very large parts can be manufactured.
Support structures are not required in Binder Jetting, leading to higher productivity, especially when compared to other metal 3D printing technologies.
New metal Binder Jetting systems that are planned for release in 2018 are expected to push the capabilities of this technology forwards.
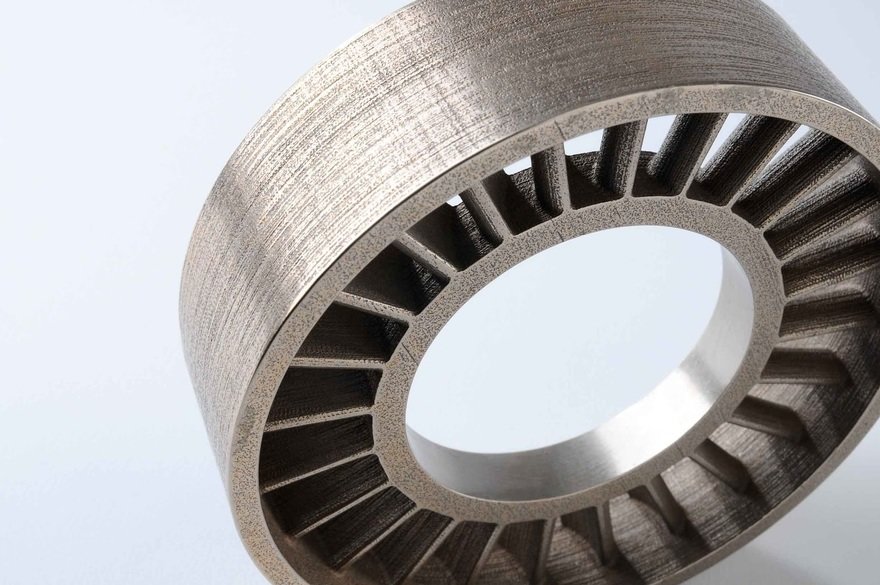
Here is a summary of other important Binder Jetting printer parameters:
-Typical build size: 400 x 250 x 250 mm (up to 800 x 500 x 400 mm)
-Support structures: Not required
-Typical layer thickness: 50 - 100 µm
-Binder Jetting materials: Metals, full-color sandstone, silica sand - see more.
For more details on designing parts for Binder Jetting, visit the article here.
In conclusion
Designing for a specific 3D printing technology requires knowledge of the basic mechanics of each process. Familiarizing yourself with the basic principles of 3D printing will help you get more out of your designs.
For those that want to learn more, The 3D Printing Handbook helps you master all the key aspects of 3D printing. It is designed to read unlike any other engineering book, full of easy-to-understand diagrams and inspiring visuals and will help you find the right 3D printing process for all of your designs.
*******
3D Hubs is the world’s largest network of manufacturing services. With production facilities connected in over 140 countries, the 3D Hubs online platform helps you find the fastest and most price competitive manufacturing solution near you. Founded in 2013, the network has since produced more than 1,000,000 parts locally, making it the global leader in distributed manufacturing.
http://www.core77.com/posts/74401/Design-Rules-for-3D-Printing