#HTE
How to Select the Right 3D Printing Process
Introduction
One of the most challenging tasks facing designers and engineers new to 3D printing is having to navigate through the vast number of 3D printing processes and materials to find the solution that is best for their application.
In this article, we present several easy-to-use tools to help you select the right 3D printing process for your application.
Overview of the 3D Printing processes
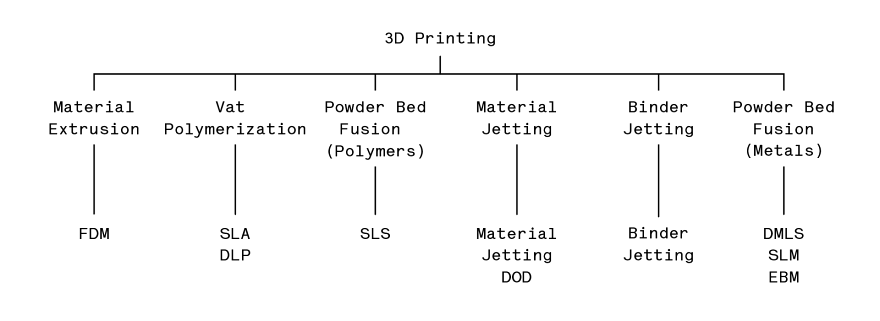
The ISO/ASTM 52900 Standard was created in 2015 to standardize all terminology and classify each of the different methods of 3D printing. A total of seven process categories were established.
Each of these and the associated process description are presented in the following table:
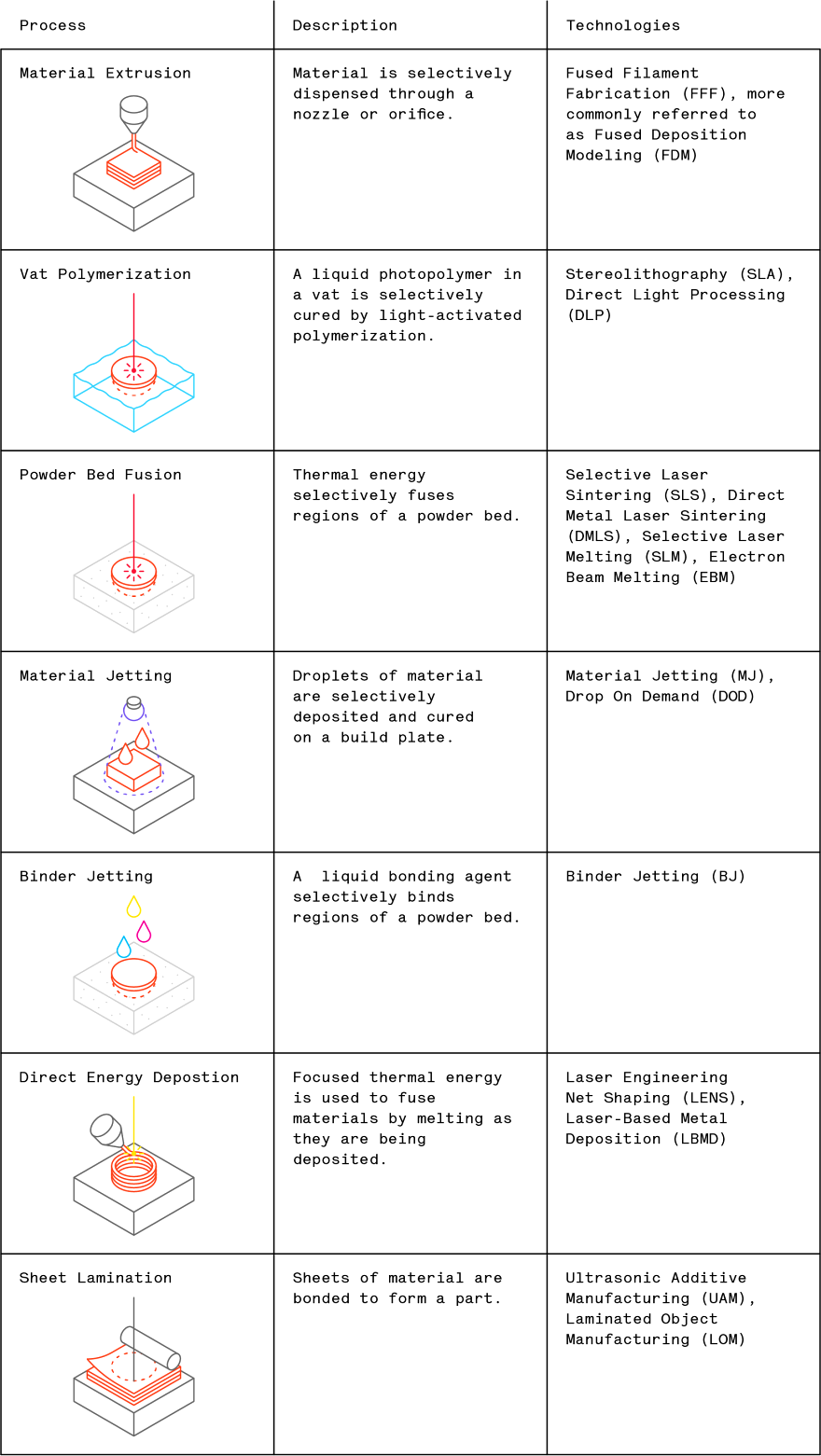
Of these technologies, Fused Deposition Modeling (FDM) and Stereolithography (SLA) are the most easily accessible and cost-competitive options, as both industrial and desktop systems are widely available.
For high-end polymer applications, Selective Laser Sintering (SLS) and Material Jetting (MJ) are popular options, while SLM and DMLS or Binder Jetting can produce 3D printed metal parts.
With all these options, how can a designer decide which process is best for an application?
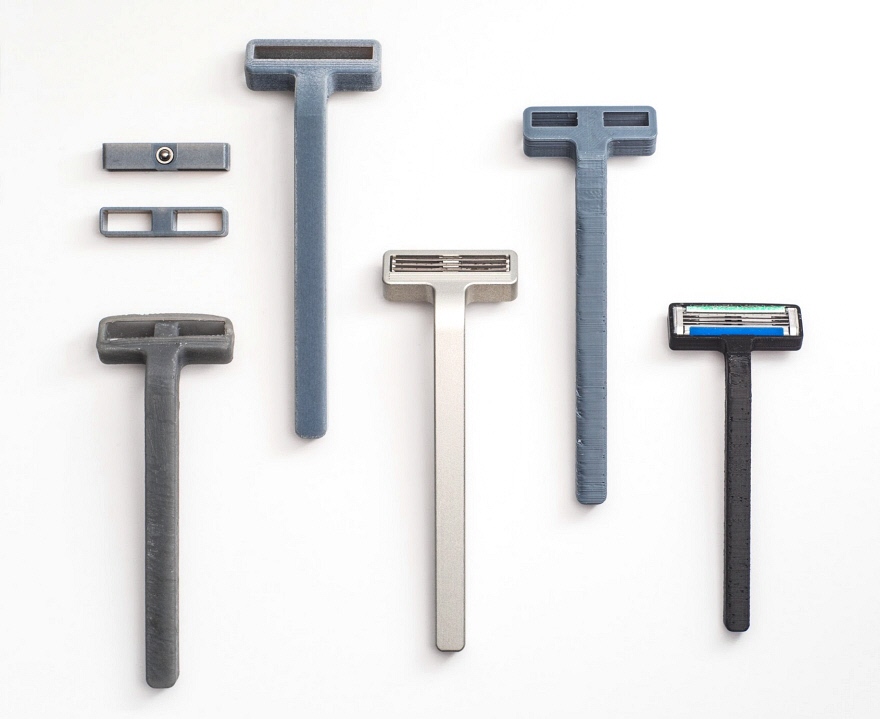
Decision making tools
Let’s jump right in…
“With 3D printing, it is particularly important to determine early in the selection process whether the main design criteria are based on functional requirements or visual appearance. This greatly simplifies the selection process.”
To further simplify things and make the information in this article actionable, some high-level generalizations are introduced as useful starting points for the decision making process:
— Functional polymer parts: compare FDM vs. SLS (thermoplastics). SLS parts have superior physical properties, but FDM is more cost-effective. For parts with highly complex geometry, SLS is generally the only option.
— Visual polymer parts: For parts where aesthetics are important, we suggest to compare SLA vs. Material Jetting (thermoset). They both can produce parts with injection-mold like appearance, but Material Jetting has the upper hand in terms of surface finish and dimensional accuracy, but at a significantly higher price point.
—Metal parts: compare Binder Jetting vs. DMLS/SLM (metal powders). DMLS/SLM parts have excellent mechanical properties and dimensional accuracy, while Binder Jetting can be up to 10x cheaper and is usually the only option for producing large metal parts.
Note: Use the above guidelines as a starting point, there are many situations in which these generalized rules do not apply. For example, SLA or Material Jetting can produce functional parts from speciality materials (such as low-run injection molds and hearing aids). Also, low-cost visual prototyping can be often be done using FDM, for example.
Functional applications
If functionality is the main goal, the flowchart below can help you identify the most suitable 3D printing process based on your main requirement:
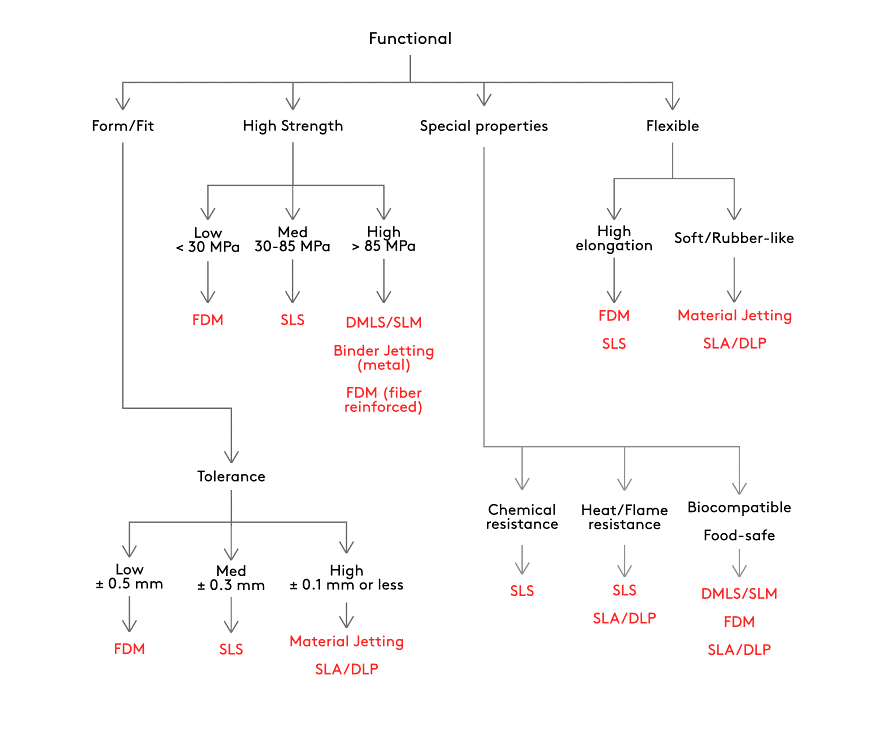
Form & Fit:
When designing a part or prototype that will fit with other components, such as enclosures, it is important to define the necessary level of tolerance. Generally, selecting a process with higher dimensional accuracy and high detail will increase the cost.
An alternative to selecting a process with higher dimensional accuracy is to finish features with critical dimensions after 3D printing (for example by drilling holes or tapping threads).
High Strength:
Overall part strength depends on different mechanical and physical properties. To simplify the selection, the material Tensile Strength can be used as guidance.
When high strength and stiffness are required, metal 3D printing or FDM printing reinforced with continuous carbon fibers are the best solutions.
Special Properties:
Engineering 3D printing materials, like ULTEM, are available with special properties, such as flame retardant and chemical or heat resistant, as well as biocompatible or food-safe certified materials.
High Flexibility:
Flexibility can be defined as either a high elongation at break (flexibility), where common thermoplastics such as TPU are available in SLS and FDM, or as low hardness, where materials with a rubber-like feel are available for SLA and Material Jetting.
Visual appearance
When visual appearance is the main concern, then the 3D printing process selection can be simplified using the flowchart below:
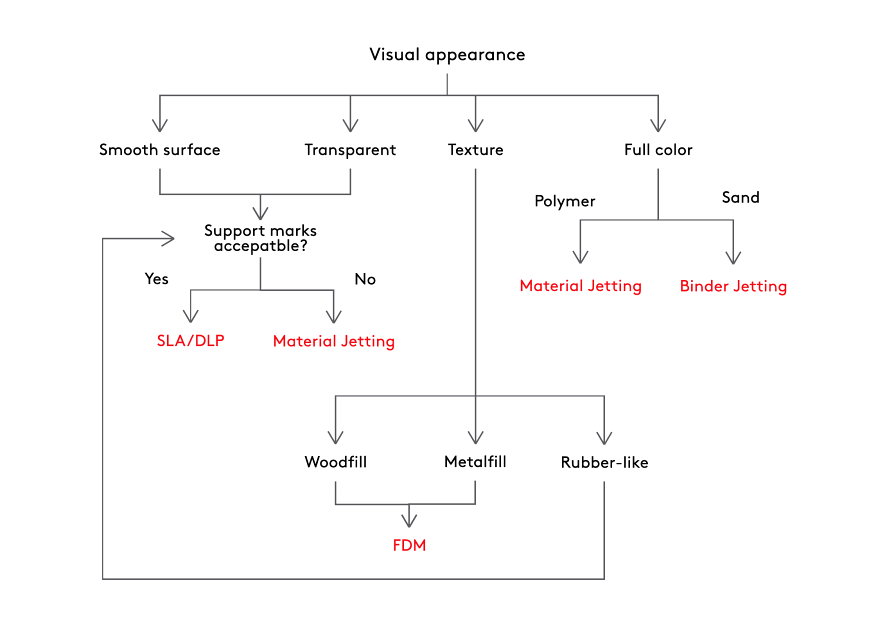
Smooth Surface:
Both SLA and Material Jetting can produce parts with smooth, injection-mold-like surface finish.
The main difference between the two processes (apart from the cost) is that support in Material Jetting is soluble, while in SLA the support structures to be removed manually after printing, leaving small marks on the surface that need to be post processed (sanded or polished).
Transparency:
Material Jetting can produce fully transparent parts with a glass-like appearance, while SLA parts are printed semi-transparent and can be post processed to be almost 100% optically clear.
Texture:
Parts with special texture, such as a wood-like or metal-like finish, can be printed using woodfill or metalfill FDM filaments.
Rubber-like parts are soft (shore hardness < 70A) and can bend and compress, but lack the performance of true rubber.
Full Color:
Material Jetting and Binder Jetting are the only 3D printing processes that currently offer full-color printing capabilities.
Material Jetting generally is the preferred process, as it offers materials with better physical properties. Multi-color 3D selfies (figurines) are often printed using Binder Jetting, as it is cheaper.
Reference table
The following table can be used for reference to compare between the different 3D printing technologies:
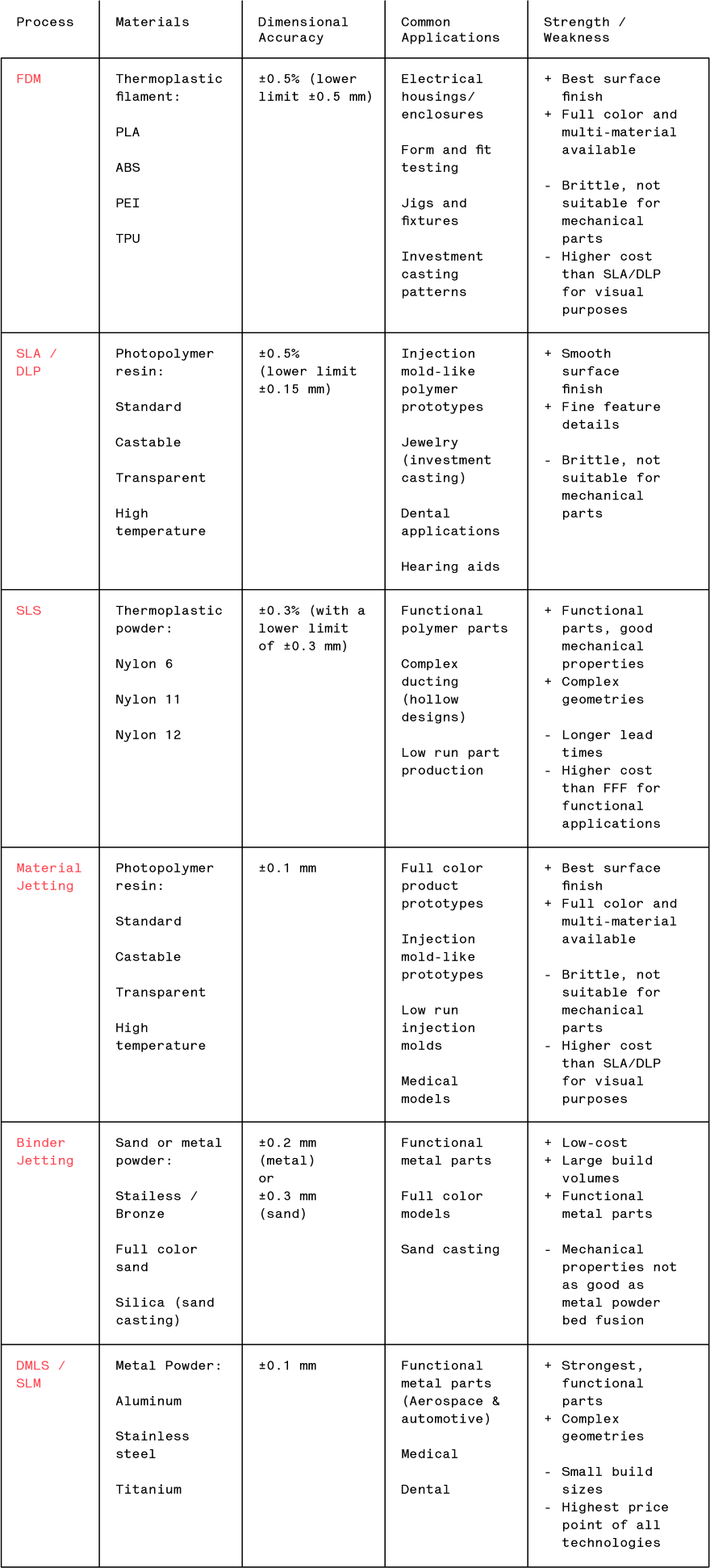
Conclusions
The guidelines and tables of this article should already give you a basic understanding and reference for choosing between the different 3D printing processes.
For those that want to learn more, The 3D Printing Handbook helps you master all the key aspects of 3D printing. It is designed to read unlike any other engineering book, full of easy-to-understand diagrams and inspiring visuals and will help you find the right 3D printing process for all of your designs.
*****
3D Hubs is the world’s largest network of manufacturing services. With production facilities connected in over 140 countries, the 3D Hubs online platform helps you find the fastest and most price competitive manufacturing solution near you. Founded in 2013, the network has since produced more than 1,000,000 parts locally, making it the global leader in distributed manufacturing.
http://www.core77.com/posts/71172/How-to-Select-the-Right-3D-Printing-Process