#HTE
Reader Submitted: Vaquform: Desktop Vacuum Forming Comes of Age for the Modern Maker
I’m an industrial designer by trade, so making models and prototypes is big part of what I do. I have amassed many tools over the years including a laser cutter, a couple of CNC routers and several 3D printers. I also have the usual complement of shop tools, as well as somewhat exotic equipment like a pressure chamber and a curing oven. It’s fair to say that I can pretty much fabricate anything out of any material using the various tools and techniques at my disposal.
One fabrication method that I’ve relied on heavily in the years I’ve been doing design work is vacuum forming. Way before there was 3D printing, back when everything had to be made with a steady hand, it was my secret-sauce technique for making plastic parts.
That said, I was always on the lookout for ways to make work go faster. I still remember how I was instantly enamored with 3D printing (or ‘rapid prototyping’ as it was called then) when I saw it for the first time on Discovery Channel. I was the guy you’d expect to rush out and buy a 3D printer when prices started to drop. But I didn’t. I was never impressed by the output quality of filament-type 3D printers, and stereolithography printers were still expensive then.
I caved in 2013 and bought myself a Makerbot Replicator. And boy, did I love it. I was kicking myself for not getting one sooner. It wasn’t that the quality exceeded my expectations—it didn’t. Prints always require some kind of post-processing. But by buying the machine I had inadvertently given myself the precious gift of time—yes, time. The 3D printer became a shop assistant that churned out parts at my bidding, leaving me free to do other tasks. That robotic minion was soon joined by two more. They all could work 24/7. And none of them took a salary.
Finding creative uses for 3D printing improved my productivity. One of these uses brought me full circle: making vacuum forming tools/molds. 3D printing allows for complex geometry, but print speeds could be excruciatingly slow. Vacuum forming is fast, but without a tool, it is useless. The two technologies working in tandem, though, was a dream. Print the tool on a 3D printer and make the final parts on the vacuum former—it was a match made in nerd heaven.
3D printers have become ubiquitous thanks to their media abetted popularity. Vacuum forming, in contrast, remains rather esoteric. It doesn’t help that vacuum forming technology has pretty much languished, untouched by innovative thinking. I thought I could change that by bringing fresh ideas to the table, or rather, the tabletop.
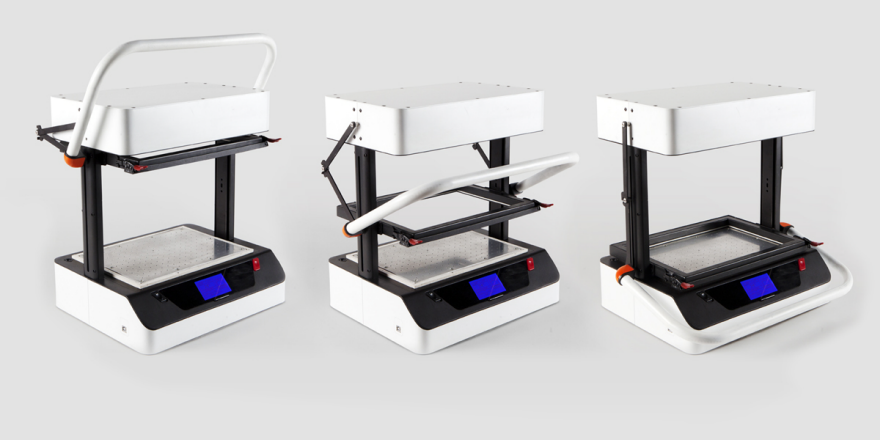
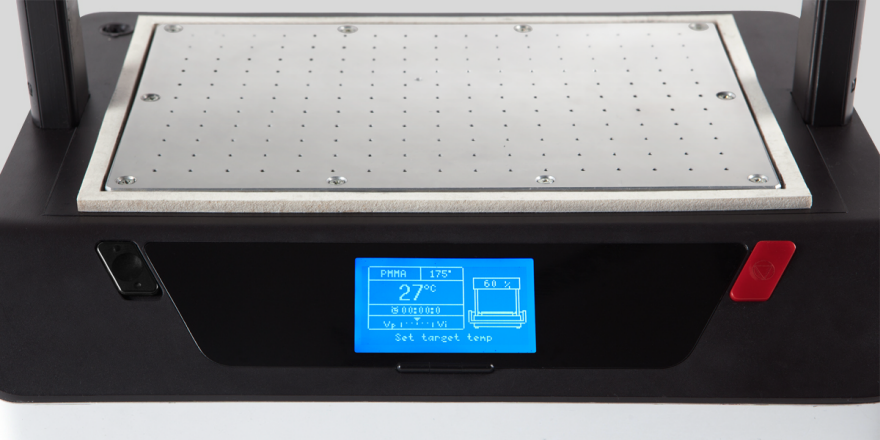
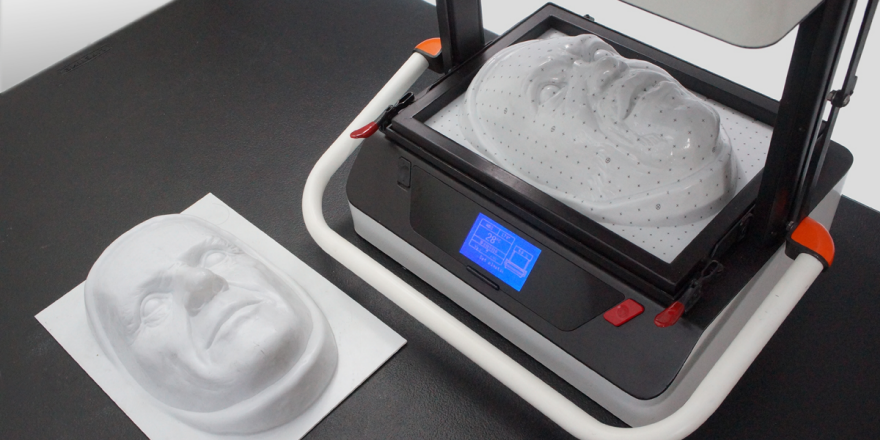
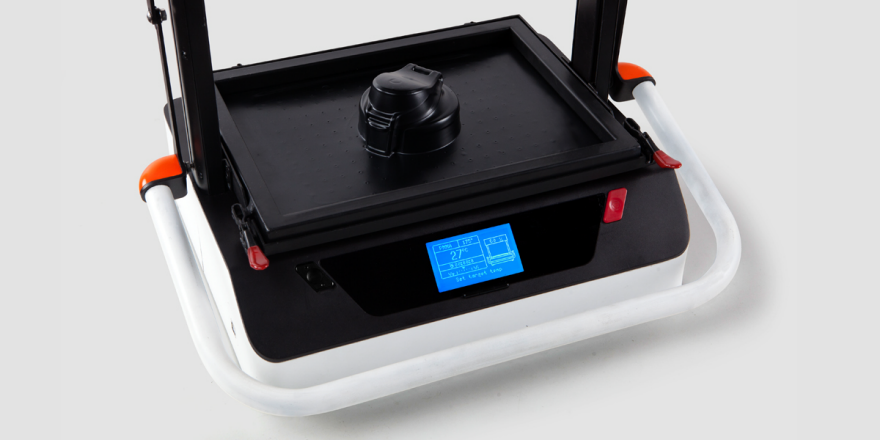
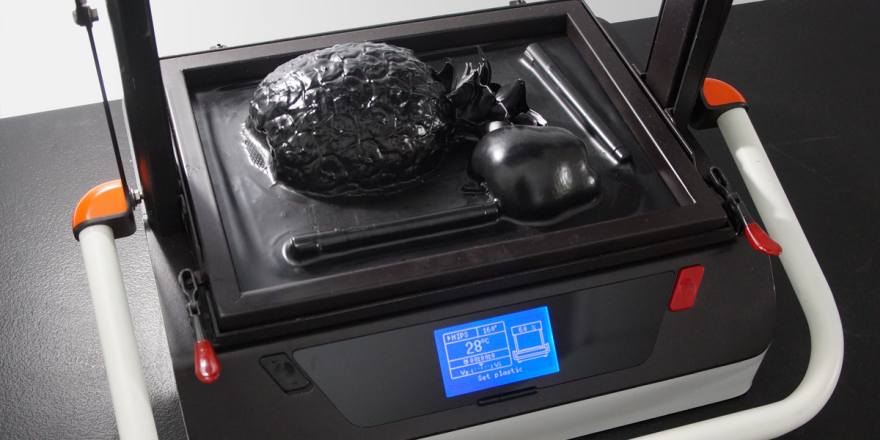
http://www.core77.com/projects/59110/Vaquform-Desktop-Vacuum-Forming-Comes-of-Age-for-the-Modern-Maker