The medical device space is a slow-moving behemoth bogged down by regulation and in need of disruptive ideas and design innovation. In recent years, we’ve seen a number of interesting ideas emerge in the space from designing handwashing to the ways that rapid prototyping has transformed prosthetics. As the medical industry braces for radical change, the way people administer and receive medical care will also shift, demanding different products and systems.
Core77 recently spoke with Bresslergroup and Eastman Innovation Lab about the trends and material innovations informing the next wave of medical device design. Materials matter in the future of medical device design—the space cannot progress without practical, safe and durable materials to accommodate new ways of working.
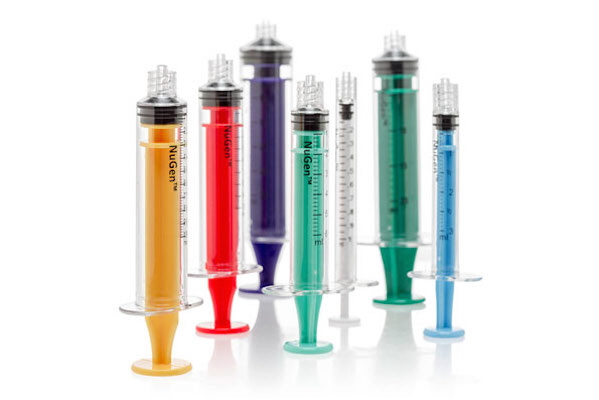
In her role as Market Development Manager for specialty plastics in medical devices at Eastman, Ellen Turner has a keen eye for these trends. Turner leads global strategy by understanding what the market needs and what new products Eastman can develop to fill that gap. She works in collaboration with designers, design engineers and product managers to match the technical capabilities of Eastman’s materials with the product needs of the market.
Founded in 1970 as “Designs for Medicine,” Bresslergroup has medical device design in the firm’s DNA. As Mathieu Turpault, Managing Partner and Director of Design explained, Bresslergroup’s approach to medical device design is rooted in a comprehensive understanding of the history of the field while looking towards new opportunities in material and technology innovation.
SUSTAINABILITY
When it comes to material considerations for medical device design, manufacturers have two main concerns: durability and cost. Durability is especially pertinent because medical equipment is subjected to a battery of harsh chemical cleaners, varied sterilization methods and concentrated drugs. Higher durability means fewer products in landfills. As Turner explains, “the leading reason someone would take a look at Eastman Tritan is that it has less cracking and breaking when it contacts drugs or disinfectants or body fluids.” For example, a blood oxygenator has many different components that would be assembled with adhesive and solvents. A polycarbonate with higher molded-in stress could see cracking whereas a copolyester like Tritan has a very low molded-in stress and good resistance to lipids. “The ability to come in contact with multiple drugs, solvents, adhesives, flushing—all of those things in combination are very important.”
Within the life cycle of a medical product, durability can also mean cost savings. Tritan does not have the same color shift that polycarbonates or acrylics have after sterilization and there is a lower scrap rate from problems like the black specks in molded polycarbonate. “Materials make a big difference,” Turner points out. “The bigger story is, how long is that product going to last? How many of those housings are going to end up in the landfill? How many of these housings are going to look terrible? And will the patients in a hospital think less of the healthcare system that’s utilizing this brand of devices because they just don’t look clean.”
In addition, the FDA has issued warnings to stop using polycarbonates and ABS in certain applications like oncology drugs. Not only are chemicals of concern-free solutions like Tritan important for patient health, but also important for the health of the planet once products enter the waste stream—there is no BPA, BPS, halogens, antimony or metals in Tritan. “It’s not even a plasticized solution,” Turner explains. “There are no orthophthalate plasticizers—there are a lot of people looking to match up their environmentally-preferred purchasing plan and Tritan doesn’t have any of those chemicals.”
HOSPITALS OF THE FUTURE
Cost pressure is also spurring medical technology manufacturers to look five to ten years out to speculate on the hospitals of the future. “All of them are coming to the conclusion that care is shifting away from traditional hospitals and doctors’ offices and moving more towards home care or point of care,” Turpault notes. Research shows that healthcare costs go down considerably the less time people spend in the hospital.
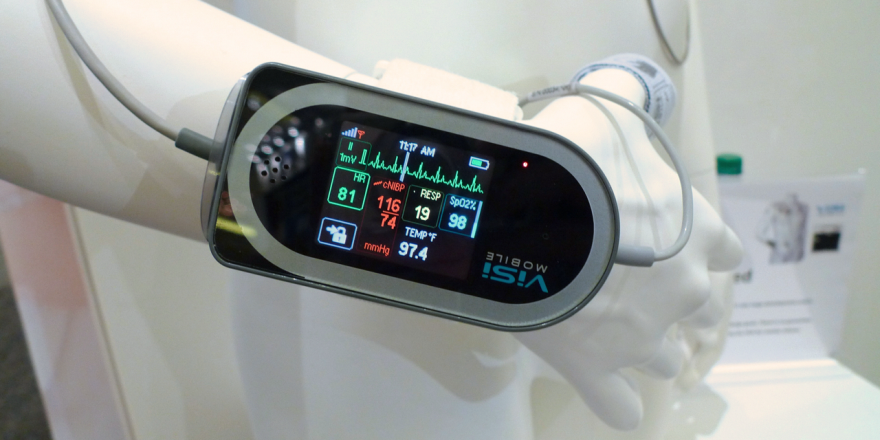
To this end, new models of healthcare delivery are emerging and demanding new product solutions. What that means for design is that there’s real work to be done in researching human factors for home healthcare and translating that knowledge to a new and category of home med tech. Using the example of the recent outrage around the EpiPen auto injector price hike, Turner underlines the fact that, “the way the drug is delivered can be just as important to a drug company as the drug itself.”
CONSUMER EXPECTATIONS
As medical devices expand beyond traditional physical product design, expect to see broader and richer user experience. “Digital experiences enable you to teach people how to use the product the right way from the get go,” Turpault underlines. “Then it gives them a way to track their performance and communicate back with healthcare professionals.”
It’s important to note that, just because the user experience is going to require embedded technologies, doesn’t mean that the material choices for the housing no longer carry as much importance. As medical devices push into the consumer space, “effort is being spent on the tactile experience so that you have a very physical connection to the product,” Turpault points out. Custom textures, finishes and tactility can really differentiate a product but the challenge remains to balance those needs with the “burden of cleaning and sterility.” Copolyesters like Tritan address the challenge with lower molded-in stress and higher chemical resistance offering a solution for designers seeking to differentiate their product while standing up to safety standards.
As consumer expectations begin to drive the development and design of medical devices, it’s important to remember that we all have a personal stake in medical device design. As Turner reminds us, “When you combine the ability to provide a material solution that enables a cleaner, better, safer way of infusing drugs for patients along with the cost saving measures that come with using a material that lasts longer in harsh hospital environments—it not only makes sense, it helps fuel your passion.”
Learn more about Tritan and the ways that #MaterialsMatter at innovationlab.eastman.com.
http://www.core77.com/posts/56848/Materials-Matter-How-Consumer-Expectations-and-Sustainability-are-Shaping-Medical-Device-Design-for-the-Future