#HTE
Creating Complicated Shapes by Hand, Faster than a 3D Printer, Using Primitive Tools
I became so fascinated by Jeremy Atkinson’s strange-looking tools (seen in the “Tales of Forgotten Crafts” video) that I had to look into them. And I’m glad I did. Because those three ancient, weirdly-shaped pieces of iron surprisingly enable Atkinson to perform a task that would be a challenge to any modern-day designer/builder wielding any number of power tools.
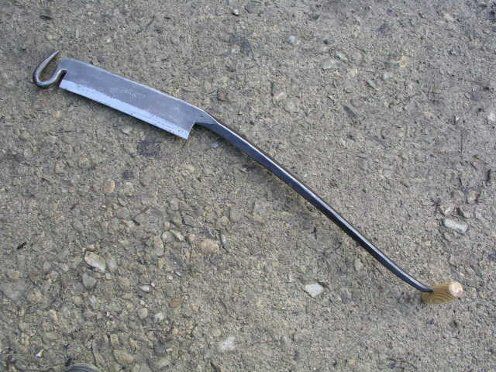
That task is to create—quickly, no less—a complex, compound-curved, undercut-riddled three-dimensional object in an occasionally uncooperative material. The first kicker is that this object, known as a clog, must then mesh perfectly with a rather crucial piece of human anatomy, the feet on which all of our weight rests. The second kicker is that Atkinson can make these by hand faster than you could possibly draw them in CAD and 3D print them.
First off, let’s look at these strange tools, which resemble medieval torture devices:
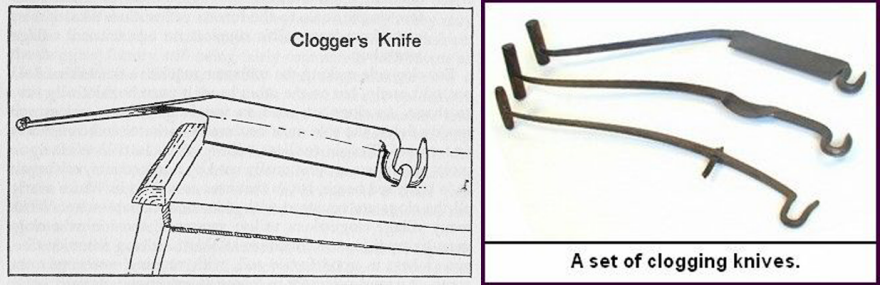
You can’t help but notice the wicked-looking hook on the end of them. That hook is what makes these tools modular. That functionality becomes more apparent when you look at a clog maker’s workbench:
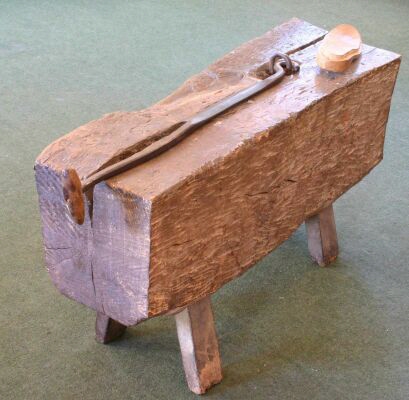
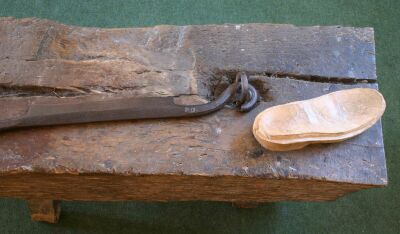
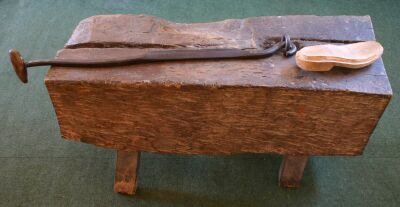
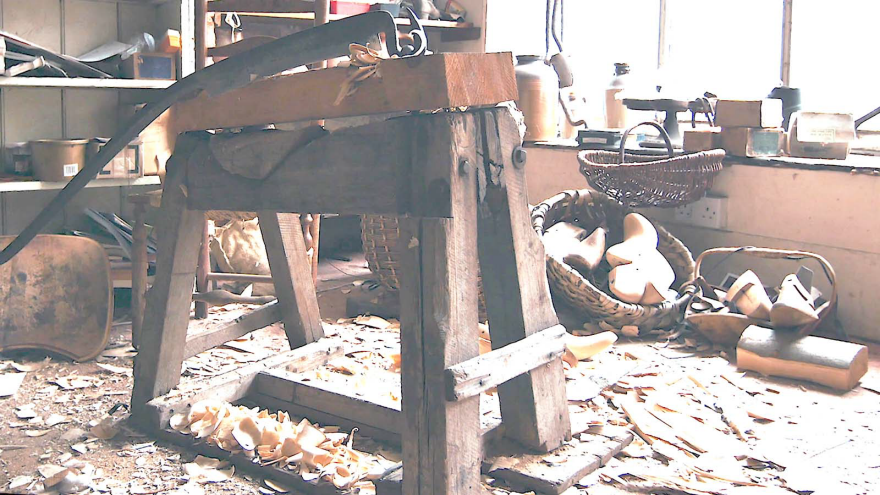
A craftsperson can insert the hook end of the tool of their choice into that eyelet, creating a pivot point at one end.
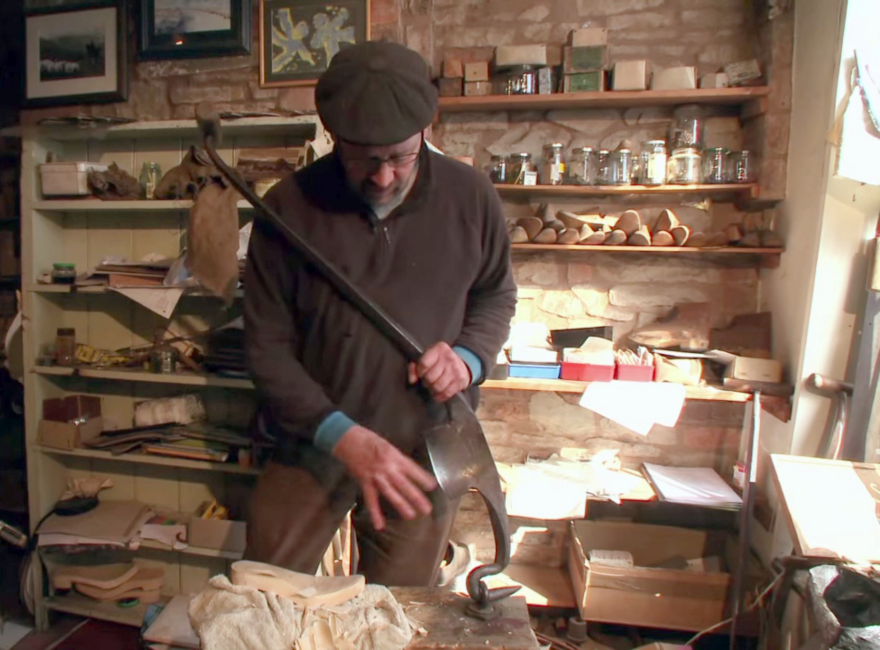
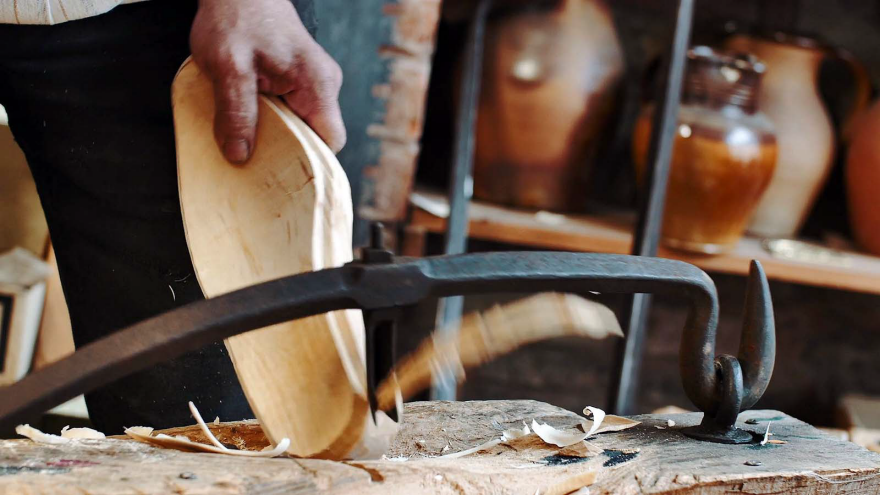
The eyelet is captive but not fixed; it can rotate freely and also has some slack in the up-down direction. Thus the craftsperson has both leverage and a relatively free range of motion with which to swing the blade.
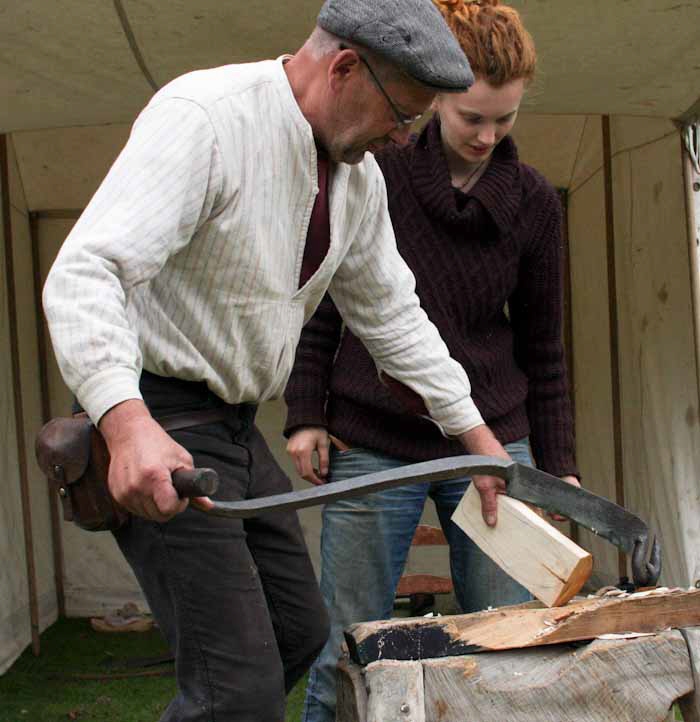
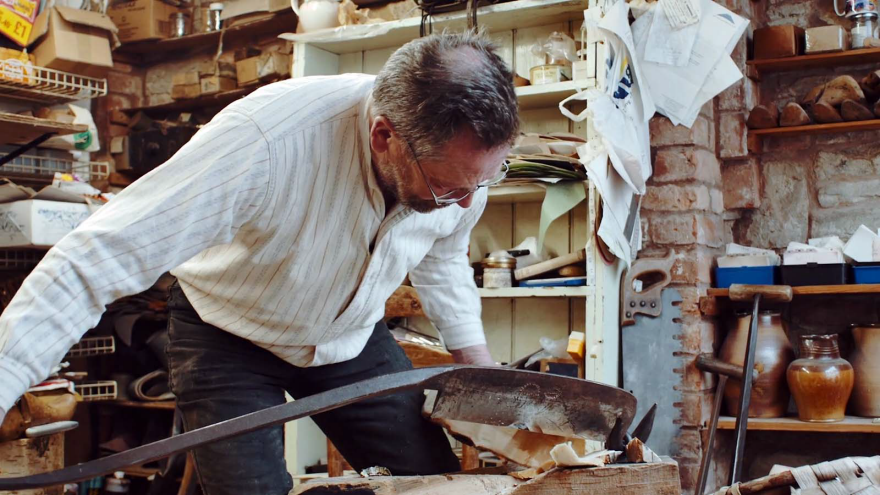
You now see why these are sometimes collectively referred to as “pivot knives.” Also, each of the blades has a different function. Take a look at the image below:
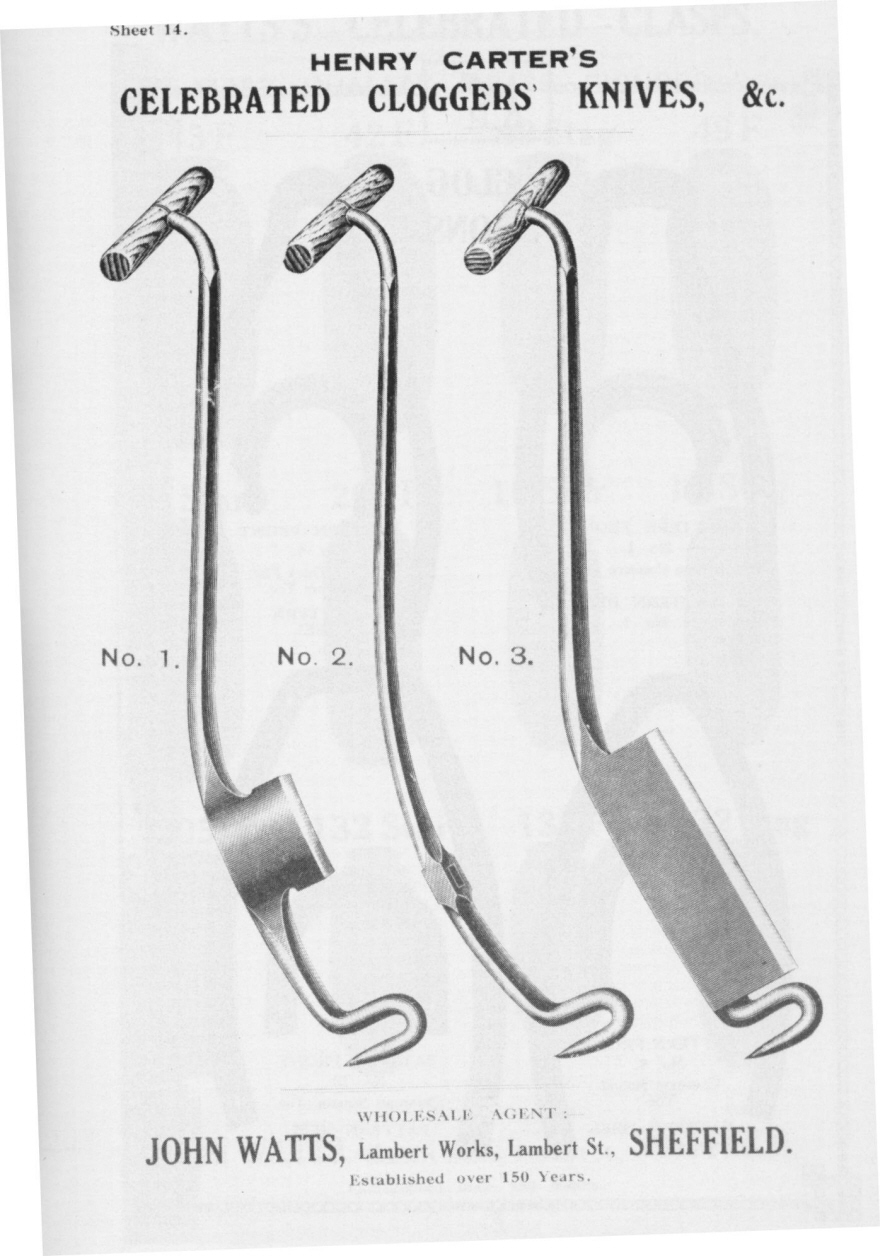
Here’s some explanation of what they do, in the order in which they are used: No. 3 above is called a stock knife and features a heavy straight blade.
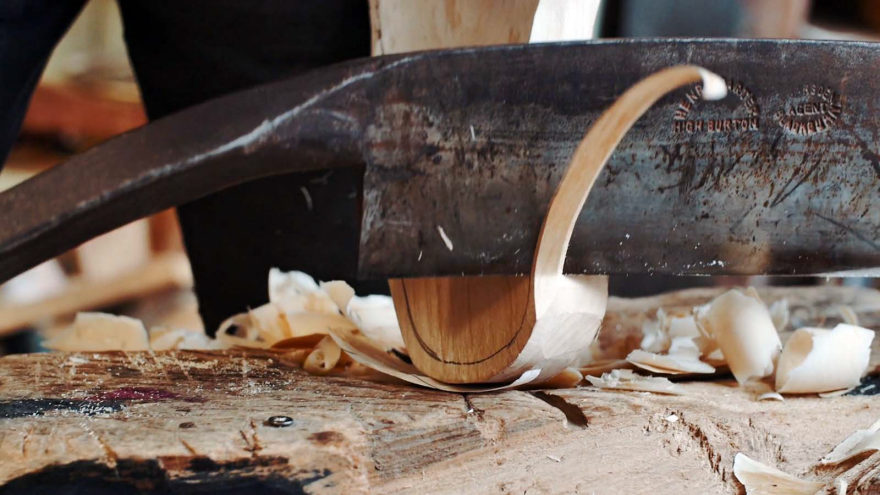
No. 1 above is called a hollower and has a curved blade that can be used to create concave surfaces.
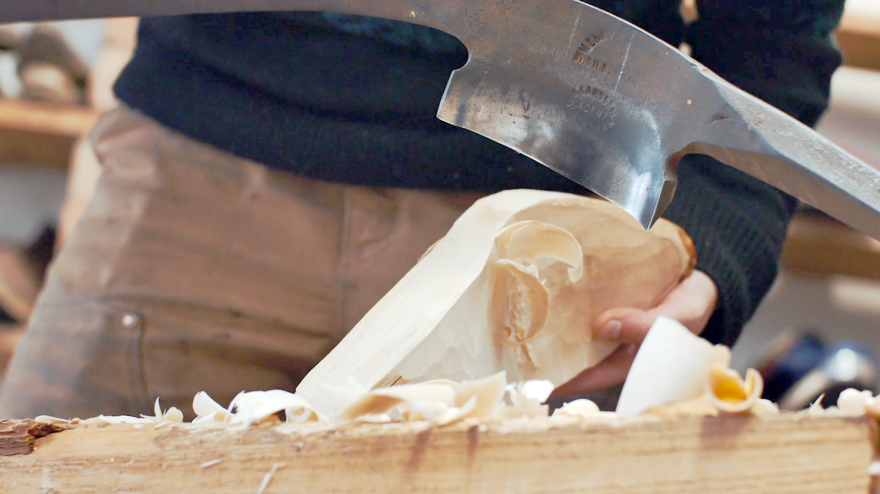
No. 2 above is called a gripper bit and is missing the blade in the black-and-white diagram above; in that image, north of the hook, you can make out the rectangular aperture into which a v-shaped blade is fastened. This v-shaped blade enables the craftsperson to carve what is essentially a rabbet, albeit one that curves and winds 360 degrees and through three dimensions.
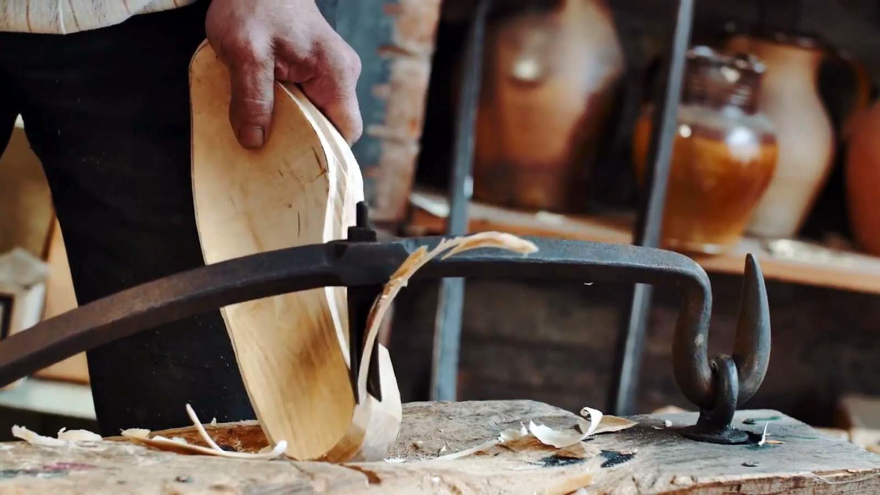
If the functions are not clear by the descriptions, you’ll swiftly grasp them by watching the videos below. As clever as their designs are, the tools are nothing without the skilled hands to work them, and here Jeremy Atkinson demonstrates his craft. For instance, would you think that you could rough out an item like this…
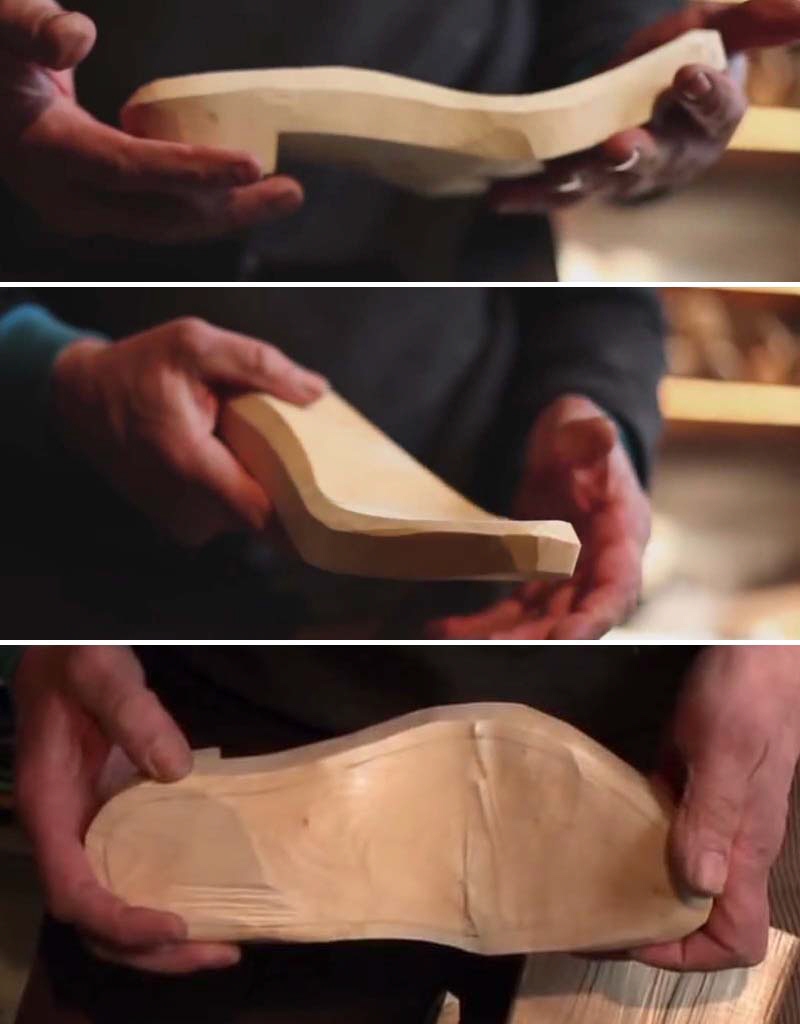
…in five to ten minutes? Atkinson can, as you’ll see here:
I was surprised to see him break out the Japanese-style Silky pull saw for the heel. But unsurprising is Atkinson’s obvious lifelong experience in working with wood grain and great manual skill: You can see him swiftly but ever-so-gently start a light cut going with the grain, then suddenly accelerate with great force and accuracy as he rounds a curve to go cross-grain.
In the second video, you see him using the hollower, and again his skill is apparent. But it’s when he starts deftly using the v-blade, to get that perfect ledge all around, that my mind was blown:
For someone who says “Don’t ask me the mathematical formula [about the cutting geometry], because I can’t work it out,” Atkinson’s clear explanations of how the chamfers on the back of the hollowing blade service the cuts is illuminating. I was also interested to hear that the tools are in fact composites, with raw iron handles laminated to high-carbon steel blades.
Overall, I was as impressed by Atkinson’s head as much as I was impressed by his hands and the tools. His sharp understanding of the anatomy of the human foot and his keen grasp of how two-dimensional outlines must be translated into 3D space surely rival that of any modern-day sneaker designer.
It is a shame he is due to retire, pending the forthcoming loss of manual dexterity he touched on in the “Forgotten Crafts” video. At that time, Nike or one of the larger footwear companies really ought to hire him as a consultant. I’m sure a lot of his knowledge would apply, and that subsequent generations would benefit from his experience.
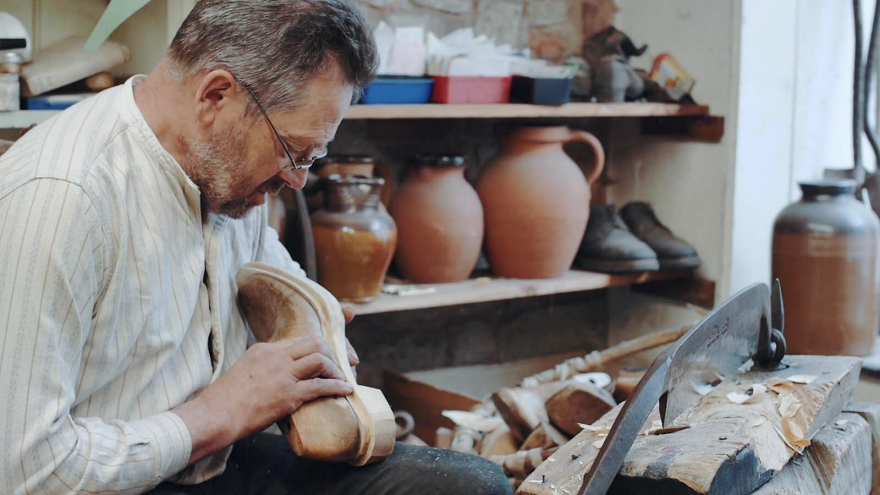
http://www.core77.com/posts/47280/Creating-Complicated-Shapes-by-Hand-Faster-than-a-3D-Printer-Using-Primitive-Tools